Biyokütlenin mineral enerjiye göre kül, nitrojen ve kükürt gibi zararlı maddelerin daha az olması nedeniyle, büyük rezervlere sahip, iyi karbon aktivitesine sahip, kolay tutuşabilen ve yüksek uçucu bileşen özelliklerine sahiptir.Bu nedenle biyokütle çok ideal bir enerji yakıtıdır ve yanma dönüşümü ve kullanımına çok uygundur.Biyokütlenin yakılmasından sonra kalan kül, fosfor, kalsiyum, potasyum ve magnezyum gibi bitkilerin ihtiyaç duyduğu besinler açısından zengin olduğundan tarlaya geri dönmek için gübre olarak kullanılabilir.Biyokütle enerjisinin muazzam kaynak rezervleri ve benzersiz yenilenebilir avantajları göz önüne alındığında, şu anda dünya çapındaki ülkeler tarafından ulusal yeni enerji gelişimi için önemli bir seçim olarak kabul edilmektedir.Çin Ulusal Kalkınma ve Reform Komisyonu, "12. Beş Yıllık Planda Mahsul Samanının Kapsamlı Kullanımına İlişkin Uygulama Planı"nda, samanın kapsamlı kullanım oranının 2013 yılına kadar %75'e ulaşacağını ve 2013 yılına kadar %80'i aşmaya çalışacağını açıkça belirtmiştir. 2015.
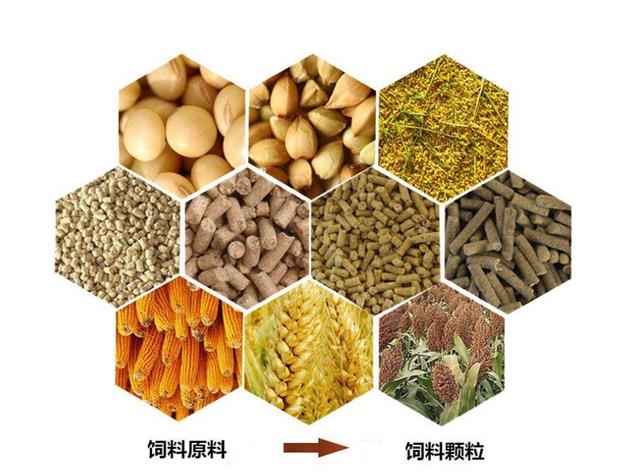
Biyokütle enerjisinin yüksek kaliteli, temiz ve kullanışlı enerjiye nasıl dönüştürüleceği çözülmesi gereken acil bir sorun haline gelmiştir.Biyokütle yoğunlaştırma teknolojisi, biyokütle enerjisinin yakılmasının verimliliğini artırmanın ve taşımayı kolaylaştırmanın etkili yollarından biridir.Şu anda, iç ve dış pazarlarda dört yaygın yoğun şekillendirme ekipmanı türü bulunmaktadır: spiral ekstrüzyon parçacık makinesi, piston damgalama parçacık makinesi, düz kalıp parçacık makinesi ve halka kalıp parçacık makinesi.Bunlar arasında halka kalıp pelet makinesi, çalışma sırasında ısıtmaya gerek olmaması, hammadde nem içeriğine yönelik geniş gereksinimler (%10 ila %30), büyük tek makine çıkışı, yüksek sıkıştırma yoğunluğu ve iyi performans gibi özellikleri nedeniyle yaygın olarak kullanılmaktadır. etki oluşturuyor.Ancak bu tip pelet makinelerinin genel olarak kalıbın kolay aşınması, servis ömrünün kısa olması, bakım maliyetlerinin yüksek olması, değiştirilmelerinin zahmetli olması gibi dezavantajları bulunmaktadır.Halka kalıp pelet makinesinin yukarıdaki eksikliklerine yanıt olarak yazar, şekillendirme kalıbının yapısında yepyeni bir iyileştirme tasarımı yapmış ve uzun servis ömrüne, düşük bakım maliyetine ve uygun bakıma sahip set tipi bir şekillendirme kalıbı tasarlamıştır.Bu arada bu makale, çalışma süreci sırasında şekillendirme kalıbının mekanik bir analizini gerçekleştirdi.
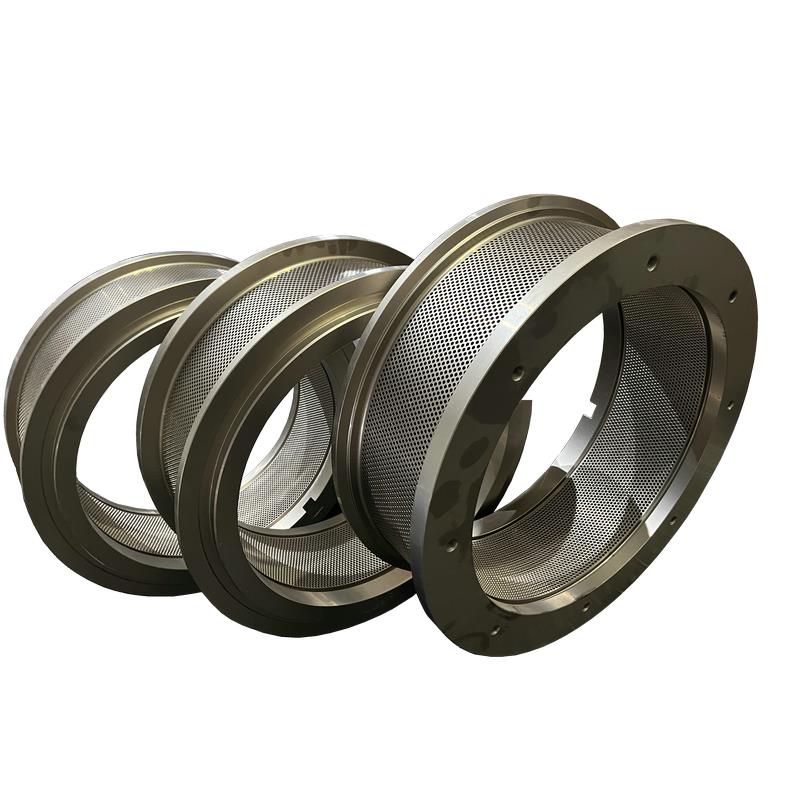
1. Halka Kalıp Granülatörü için Şekillendirme Kalıp Yapısının İyileştirme Tasarımı
1.1 Ekstrüzyon Şekillendirme Sürecine Giriş:Halka kalıp pelet makinesi iki türe ayrılabilir: halka kalıbın konumuna bağlı olarak dikey ve yatay;Hareket şekline göre iki farklı hareket şekline ayrılabilir: sabit halka kalıplı aktif baskı silindiri ve tahrikli halka kalıplı aktif baskı silindiri.Bu geliştirilmiş tasarım esas olarak aktif bir basınç silindiri ve hareket şekli olarak sabit bir halka kalıbı olan halka kalıp parçacık makinesine yöneliktir.Esas olarak iki parçadan oluşur: bir taşıma mekanizması ve bir halka kalıp parçacık mekanizması.Halka kalıbı ve basınç silindiri, halka kalıbı pelet makinesinin iki temel bileşenidir; halka kalıbının etrafına dağıtılmış birçok şekillendirme kalıbı deliği vardır ve basınç silindiri, halka kalıbının içine yerleştirilmiştir.Basınç silindiri şanzıman miline bağlanır ve halka kalıbı sabit bir brakete monte edilir.Mil döndüğünde, baskı silindirinin dönmesini sağlar.Çalışma prensibi: Taşıma mekanizması öncelikle kırılmış biyokütle malzemesini belirli bir parçacık boyutuna (3-5mm) sıkıştırma odasına taşır.Daha sonra motor, baskı silindirinin dönmesini sağlamak için ana şaftı çalıştırır ve baskı silindiri, malzemeyi basınç silindiri ile halka kalıbı arasında eşit bir şekilde dağıtmak için sabit bir hızda hareket ederek halka kalıbının malzemeyle sıkışmasına ve sürtünmesine neden olur. , baskı silindiri malzemeyle ve malzeme malzemeyle birlikte.Sıkma işlemi sırasında sürtünme nedeniyle malzemedeki selüloz ve hemiselüloz birbiriyle birleşir.Aynı zamanda, sıkıştırma sürtünmesiyle üretilen ısı, lignini yumuşatarak doğal bir bağlayıcıya dönüştürür; bu da selüloz, hemiselüloz ve diğer bileşenlerin birbirine daha sıkı bağlanmasını sağlar.Biyokütle malzemelerinin sürekli doldurulması ile şekillendirme kalıp deliklerinde sıkıştırma ve sürtünmeye maruz kalan malzeme miktarı artmaya devam etmektedir.Aynı zamanda biyokütle arasındaki sıkıştırma kuvveti artmaya devam eder ve kalıp deliğinde sürekli olarak yoğunlaşarak oluşur.Ekstrüzyon basıncı sürtünme kuvvetinden büyük olduğunda, biyokütle halka kalıbın etrafındaki kalıplama deliklerinden sürekli olarak ekstrüde edilir ve yaklaşık 1g/Cm3 kalıplama yoğunluğuna sahip biyokütle kalıplama yakıtı oluşturulur.
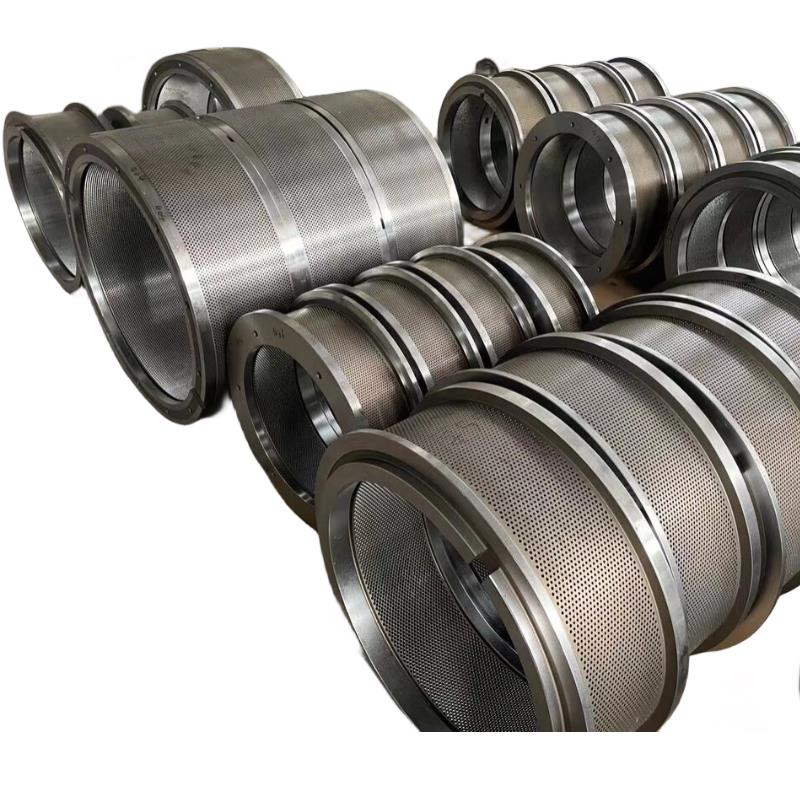
1.2 Şekillendirme Kalıplarının Aşınması:Pelet makinesinin tek makine çıkışı büyüktür, nispeten yüksek derecede otomasyona sahiptir ve hammaddelere güçlü bir şekilde uyarlanabilir.Biyokütle yoğun şekillendirici yakıtların büyük ölçekli üretimi için uygun olan ve gelecekte biyokütle yoğun şekillendirici yakıt sanayileşmesinin geliştirme gereksinimlerini karşılayan çeşitli biyokütle hammaddelerinin işlenmesi için yaygın olarak kullanılabilir.Bu nedenle halka kalıp pelet makinesi yaygın olarak kullanılmaktadır.İşlenmiş biyokütle malzemesinde az miktarda kum ve diğer biyokütle dışı yabancı maddelerin bulunması nedeniyle, pelet makinesinin halka kalıbında önemli aşınma ve yıpranmaya neden olma olasılığı yüksektir.Halka kalıbın kullanım ömrü üretim kapasitesine göre hesaplanır.Şu anda Çin'deki halka kalıbın hizmet ömrü yalnızca 100-1000 tondur.
Halka kalıbın arızası temel olarak aşağıdaki dört olguda ortaya çıkar: ① Halka kalıp bir süre çalıştıktan sonra, şekillendirme kalıbı deliğinin iç duvarı aşınır ve açıklık artar, bu da üretilen şekillendirilmiş yakıtın önemli ölçüde deformasyonuna neden olur;② Halka kalıbın şekillendirme kalıp deliğinin besleme eğimi aşınır, bu da kalıp deliğine sıkıştırılan biyokütle malzemesinin miktarında bir azalmaya, ekstrüzyon basıncında bir azalmaya ve şekillendirme kalıp deliğinin kolay tıkanmasına neden olur ve bu da kalıp deliğine yol açar. halka kalıbının arızalanması (Şekil 2);③ İç duvar malzemelerinden sonra deşarj miktarı keskin bir şekilde azalır (Şekil 3);
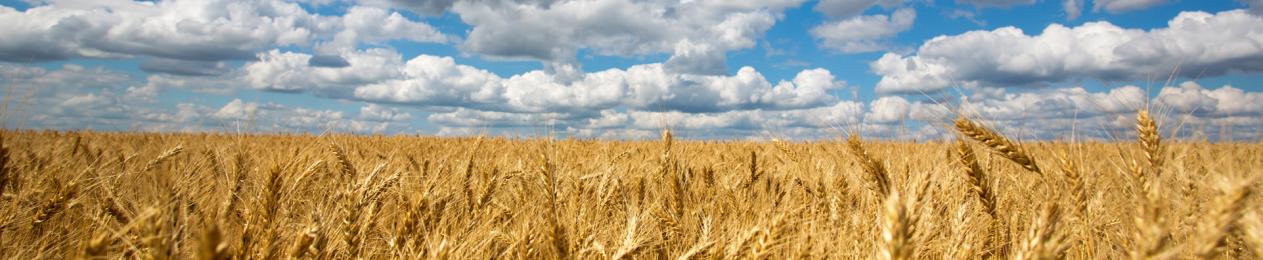
④ Halka kalıbın iç deliğinin aşınmasından sonra, bitişik kalıp parçaları L arasındaki duvar kalınlığı incelir, bu da halka kalıbın yapısal mukavemetinde bir azalmaya neden olur.En tehlikeli kısımda çatlaklar oluşmaya eğilimlidir ve çatlaklar uzadıkça halka kalıp kırılması olgusu ortaya çıkar.Halka kalıbının kolay aşınmasının ve kısa servis ömrünün ana nedeni, şekillendirme halkası kalıbının mantıksız yapısıdır (halka kalıbı, şekillendirme kalıbı delikleri ile entegredir).İkisinin entegre yapısı bu tür sonuçlara eğilimlidir: bazen halka kalıbın yalnızca birkaç şekillendirme kalıbı deliği aşındığında ve çalışamadığında, halka kalıbının tamamının değiştirilmesi gerekir, bu da yalnızca değiştirme işine rahatsızlık vermekle kalmaz, aynı zamanda büyük ekonomik israfa neden olur ve bakım maliyetlerini artırır.
1.3 Kalıp Oluşturmanın Yapısal İyileştirme TasarımıPelet makinesinin halka kalıbının ömrünü uzatmak, aşınmayı azaltmak, değiştirmeyi kolaylaştırmak ve bakım maliyetlerini azaltmak için halka kalıbın yapısında yepyeni bir iyileştirme tasarımı yapılması gerekmektedir.Tasarımda gömülü kalıplama kalıbı kullanılmış olup, geliştirilmiş sıkıştırma odası yapısı Şekil 4'te gösterilmektedir. Şekil 5, geliştirilmiş kalıplama kalıbının kesit görünüşünü göstermektedir.
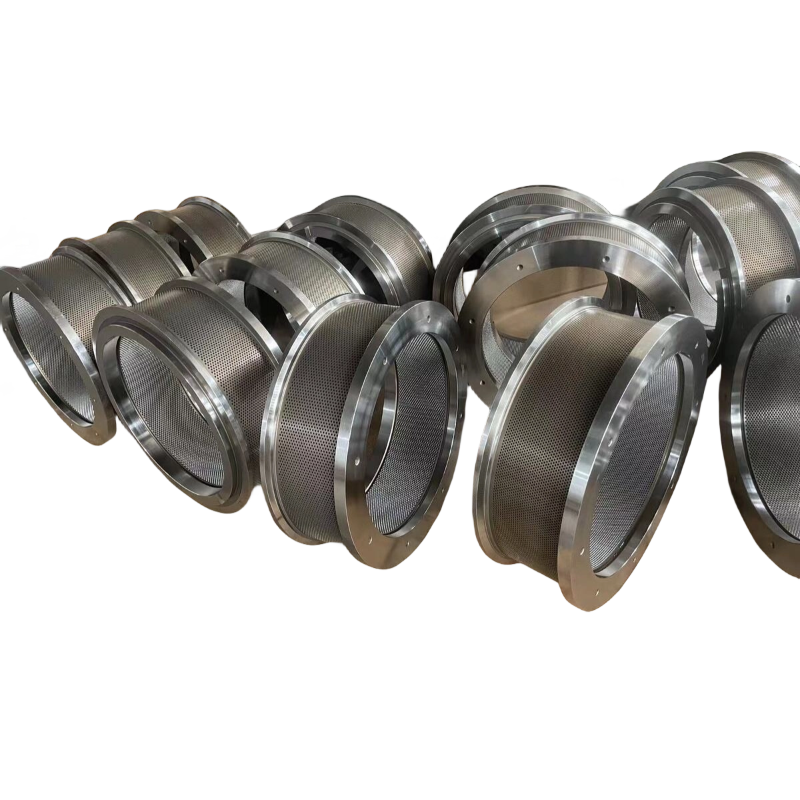
Bu geliştirilmiş tasarım esas olarak aktif basınç silindiri ve sabit halka kalıbının hareket formuna sahip halka kalıp parçacık makinesine yöneliktir.Alt halka kalıbı gövdeye sabitlenir ve iki baskı makarası bir bağlantı plakası vasıtasıyla ana mile bağlanır.Şekillendirme kalıbı alt halka kalıbı üzerine gömülür (girişimli geçme kullanılarak) ve üst halka kalıbı alt halka kalıbına cıvatalar aracılığıyla sabitlenir ve şekillendirme kalıbı üzerine kelepçelenir.Aynı zamanda, baskı silindiri yuvarlanıp halka kalıbı boyunca radyal olarak hareket ettikten sonra şekillendirme kalıbının kuvvet nedeniyle geri sıçramasını önlemek amacıyla, şekillendirme kalıbını sırasıyla üst ve alt halka kalıplarına sabitlemek için havşa başlı vidalar kullanılır.Deliğe giren malzemenin direncini azaltmak ve kalıp deliğine girmeyi daha uygun hale getirmek için.Tasarlanan şekillendirme kalıbının besleme deliğinin konik açısı 60° ile 120° arasındadır.
Şekillendirme kalıbının geliştirilmiş yapısal tasarımı, çok çevrimli ve uzun hizmet ömrü özelliklerine sahiptir.Parçacık makinesi bir süre çalıştığında sürtünme kaybı şekillendirme kalıbının açıklığının büyümesine ve pasifleşmesine neden olur.Aşınmış şekillendirme kalıbı çıkarılıp genişletildiğinde, diğer şekillendirme parçacıklarının üretimi için kullanılabilir.Bu, kalıpların yeniden kullanılmasını sağlayabilir ve bakım ve değiştirme maliyetlerinden tasarruf sağlayabilir.
Granülatörün hizmet ömrünü uzatmak ve üretim maliyetlerini azaltmak için, basınç silindiri, 65Mn gibi iyi aşınma direncine sahip yüksek karbonlu, yüksek manganezli çelik kullanır.Şekillendirme kalıbı, Cr, Mn, Ti vb. içeren alaşımlı karbürlenmiş çelikten veya düşük karbonlu nikel krom alaşımından yapılmalıdır. Sıkıştırma odasının iyileştirilmesi nedeniyle, üst ve alt halka kalıpları tarafından deneyimlenen sürtünme kuvveti. işlem, şekillendirme kalıbına kıyasla nispeten küçüktür.Bu nedenle, sıkıştırma odasının malzemesi olarak 45 çelik gibi sıradan karbon çeliği kullanılabilir.Geleneksel entegre şekillendirme halkası kalıplarıyla karşılaştırıldığında pahalı alaşımlı çelik kullanımını azaltabilir, böylece üretim maliyetlerini düşürebilir.
2. Şekillendirme kalıbının çalışma süreci sırasında halka kalıp pelet makinesinin şekillendirme kalıbının mekanik analizi.
Kalıplama işlemi sırasında, kalıplama kalıbında oluşan yüksek basınç ve yüksek sıcaklık ortamı nedeniyle malzemedeki lignin tamamen yumuşar.Ekstrüzyon basıncı artmadığında malzeme plastikleşmeye uğrar.Malzeme plastikleştirmeden sonra iyi akar, dolayısıyla uzunluk d olarak ayarlanabilir.Şekillendirme kalıbı bir basınçlı kap olarak kabul edilir ve şekillendirme kalıbı üzerindeki baskı basitleştirilir.
Yukarıdaki mekanik hesaplama analizi sayesinde, şekillendirme kalıbının içindeki herhangi bir noktada basıncı elde etmek için, şekillendirme kalıbının içindeki o noktadaki çevresel gerinimin belirlenmesinin gerekli olduğu sonucuna varılabilir.Daha sonra o konumdaki sürtünme kuvveti ve basınç hesaplanabilir.
3. Sonuç
Bu makale, halka kalıp peletleyicinin şekillendirme kalıbı için yeni bir yapısal iyileştirme tasarımı önermektedir.Gömülü şekillendirme kalıplarının kullanımı, kalıp aşınmasını etkili bir şekilde azaltabilir, kalıp çevrim ömrünü uzatabilir, değiştirme ve bakımı kolaylaştırabilir ve üretim maliyetlerini azaltabilir.Aynı zamanda, çalışma süreci sırasında şekillendirme kalıbı üzerinde mekanik analiz gerçekleştirilerek gelecekte yapılacak daha fazla araştırma için teorik bir temel sağlandı.
Gönderim zamanı: Şubat-22-2024