Zayıf su direnci, düzensiz yüzey, yüksek toz içeriği ve düzensiz uzunluk mu? Su yemi üretiminde yaygın sorunlar ve iyileştirme önlemleri
Günlük su yemi üretimimizde çeşitli sorunlarla karşılaşıyoruz. İşte herkesle paylaşabileceğiniz bazı örnekler:
1、 Formül
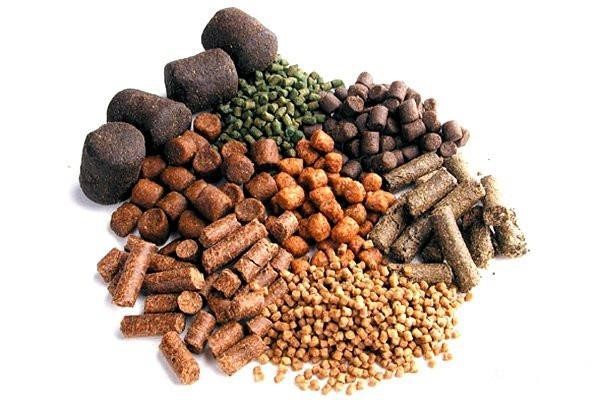
1. Balık yeminin formül yapısında, ham selüloza ait kolza tohumu küspesi, pamuk küspesi vb. gibi daha fazla çeşitte yem hammaddesi bulunur. Bazı yağ fabrikaları ileri teknolojiye sahiptir ve yağ, çok az içerikle kuru olarak kızartılır. Ayrıca, bu tür hammaddeler üretimde kolayca emilmez ve bu da granülasyon üzerinde büyük bir etkiye sahiptir. Ayrıca, pamuk küspesinin ezilmesi zordur ve bu da verimliliği etkiler.
2. Çözüm: Kolza tohumu küspesi kullanımı artırıldı ve formüle pirinç kepeği gibi yüksek kaliteli yerel malzemeler eklendi. Ayrıca, formülün yaklaşık %5-8'ini oluşturan buğday da eklendi. Yapılan ayarlamalar sonucunda, 2009 yılındaki granülasyon etkisi nispeten ideal hale geldi ve ton başına verim de arttı. 2,5 mm'lik parçacıklar 8-9 ton arasında olup, geçmişe kıyasla yaklaşık 2 tonluk bir artışa işaret ediyor. Parçacıkların görünümü de önemli ölçüde iyileşti.
Ayrıca, pamuk tohumu küspesinin ezilme verimliliğini artırmak için, ezmeden önce pamuk tohumu küspesi ve kolza küspesini 2:1 oranında karıştırdık. İyileştirme sonrasında, ezme hızı temelde kolza küspesinin ezme hızıyla aynı seviyeye geldi.
2、 Parçacıkların düzensiz yüzeyi
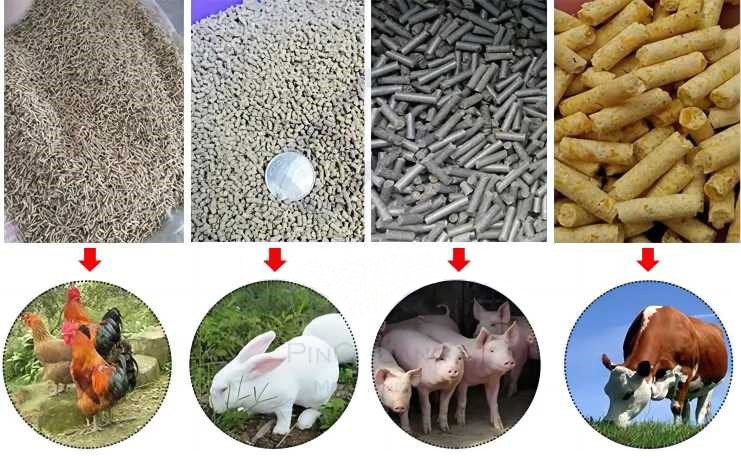
1. Bitmiş ürünün görünümü üzerinde büyük bir etkiye sahiptir ve suya eklendiğinde çökmeye meyillidir ve düşük kullanım oranına sahiptir. Bunun başlıca nedeni:
(1) Hammaddeler çok iri kırılır ve tavlama işlemi sırasında tam olarak olgunlaşmaz ve yumuşamaz ve kalıp deliklerinden geçerken diğer hammaddelerle iyi bir şekilde birleştirilemez.
(2) Ham selüloz içeriği yüksek balık yemi formülünde, tavlama işlemi sırasında ham maddede buhar kabarcıklarının bulunması nedeniyle, parçacık sıkıştırma sırasında kalıbın içi ve dışı arasındaki basınç farkından dolayı bu kabarcıklar yırtılmakta ve parçacıkların yüzeyinin düzgün olmamasına neden olmaktadır.
2. Elleçleme önlemleri:
(1) Ezme işlemini düzgün bir şekilde kontrol edin
Şu anda balık yemi üretiminde, dökme hammadde olarak 1,2 mm elek mikro tozu kullanıyoruz. Ezmenin inceliğini sağlamak için eleğin kullanım sıklığını ve çekicin aşınma derecesini kontrol ediyoruz.
(2) Buhar basıncını kontrol edin
Formüle göre, üretim sırasında buhar basıncını makul bir şekilde ayarlayın, genellikle 0,2 civarında kontrol edin. Balık yemi formülünde büyük miktarda iri lifli hammadde bulunduğundan, yüksek kaliteli buhar ve makul tavlama süresi gereklidir.
3、 Parçacıkların suya karşı direnci zayıf
1. Bu tip sorunlar günlük üretimimizde en sık karşılaşılan sorunlardır ve genellikle aşağıdaki faktörlerle ilişkilidir:
(1) Kısa tavlama süresi ve düşük tavlama sıcaklığı, dengesiz veya yetersiz tavlamaya, düşük olgunlaşma derecesine ve yetersiz neme neden olur.
(2) Nişasta gibi yetersiz yapıştırıcı malzemeler.
(3) Halka kalıbının sıkıştırma oranı çok düşüktür.
(4) Formüldeki yağ oranı ve ham elyaf hammaddelerinin oranı çok yüksektir.
(5) Ezme parçacık boyutu faktörü.
2. Elleçleme önlemleri:
(1) Buhar kalitesini iyileştirin, regülatörün bıçak açısını ayarlayın, temperleme süresini uzatın ve hammaddelerin nem içeriğini uygun şekilde artırın.
(2) Formülü ayarlayın, nişasta hammaddelerini uygun şekilde artırın ve yağ ve ham lif hammaddelerinin oranını azaltın.
(3) Gerekirse yapıştırıcı ekleyin. (Sodyum bazlı bentonit bulamacı)
(4) Sıkıştırma oranını iyileştirinhalka kalıbı
(5) Kırma inceliğini iyi kontrol edin
4、 Parçacıklarda aşırı toz içeriği
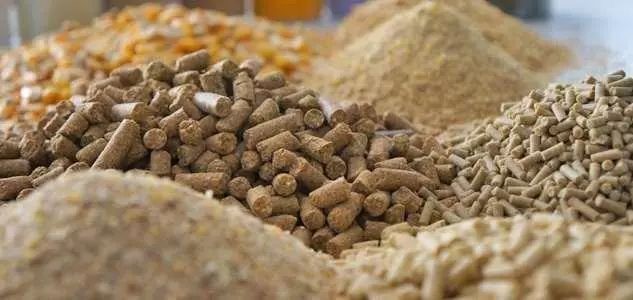
1. Genel pelet yeminin soğutulduktan sonra ve elemeden önce görünümünü sağlamak zordur. Müşteriler, peletlerde daha fazla ince kül ve toz olduğunu bildirmiştir. Yukarıdaki analize dayanarak, bunun birkaç nedeni olduğunu düşünüyorum:
A. Parçacık yüzeyi pürüzsüz değildir, kesi düzgün değildir ve parçacıklar gevşektir ve toz üretimine eğilimlidir;
B. Sınıflandırma eleği ile eksik eleme, tıkalı elek telleri, kauçuk bilyelerin aşırı aşınması, uyumsuz elek teli açıklığı, vb.;
C. Mamul depolarında çok miktarda ince kül kalıntısı bulunmaktadır ve temizlik tam olarak yapılmamaktadır;
D. Paketleme ve tartım sırasında toz giderme işleminin gizli tehlikeleri vardır;
Taşıma önlemleri:
A. Formül yapısını optimize edin, halka kalıbını makul bir şekilde seçin ve sıkıştırma oranını iyi kontrol edin.
B. Granülasyon işlemi sırasında, hammaddelerin tam olarak olgunlaşması ve yumuşaması için temperleme süresini, besleme miktarını ve granülasyon sıcaklığını kontrol edin.
C. Parçacık kesitinin temiz olmasına dikkat edin ve çelik şeritten yapılmış yumuşak bir kesme bıçağı kullanın.
D. Sınıflandırma ekranını ayarlayın ve koruyun ve makul bir ekran yapılandırması kullanın.
E. Bitmiş ürün deposunda ikincil eleme teknolojisinin kullanılması toz içerik oranını büyük ölçüde azaltabilir.
F. Bitmiş ürün deposunun ve devresinin zamanında temizlenmesi gerekmektedir. Ayrıca, paketleme ve toz giderme cihazının iyileştirilmesi gerekmektedir. Toz giderme için negatif basınç kullanmak en iyisidir, bu daha idealdir. Özellikle paketleme işlemi sırasında, paketleme işçisi paketleme terazisinin tampon haznesindeki tozu düzenli olarak temizlemelidir..
5、 Parçacık uzunluğu değişir
1. Günlük üretimde, özellikle 420'nin üzerindeki modellerde, kontrol konusunda sıklıkla zorluklarla karşılaşıyoruz. Bunun nedenleri kabaca şöyle özetlenebilir:
(1) Granülasyon için besleme miktarı eşit değildir ve temperleme etkisi büyük ölçüde dalgalanmaktadır.
(2) Kalıp silindirleri arasında tutarsız boşluk veya halka kalıbı ile basınç silindirlerinin aşırı aşınması.
(3) Halka kalıbının eksenel yönünde, her iki uçtaki boşaltma hızı, ortadakinden daha düşüktür.
(4) Halka kalıbının basınç düşürücü deliği çok büyüktür ve açılma oranı çok yüksektir.
(5) Kesici bıçağın konumu ve açısı makul değildir.
(6) Granülasyon sıcaklığı.
(7) Halka kalıp kesme bıçağının tipi ve etkili yüksekliği (bıçak genişliği, genişlik) bir etkiye sahiptir.
(8) Aynı zamanda, sıkıştırma odasının içindeki hammaddelerin dağılımı eşit değildir.
2. Yem ve peletlerin kalitesi genellikle iç ve dış kalitelerine göre analiz edilir. Bir üretim sistemi olarak, yem peletlerinin dış kalitesiyle ilgili faktörlere daha fazla maruz kalıyoruz. Üretim açısından bakıldığında, su yemi peletlerinin kalitesini etkileyen faktörler kabaca şu şekilde özetlenebilir:
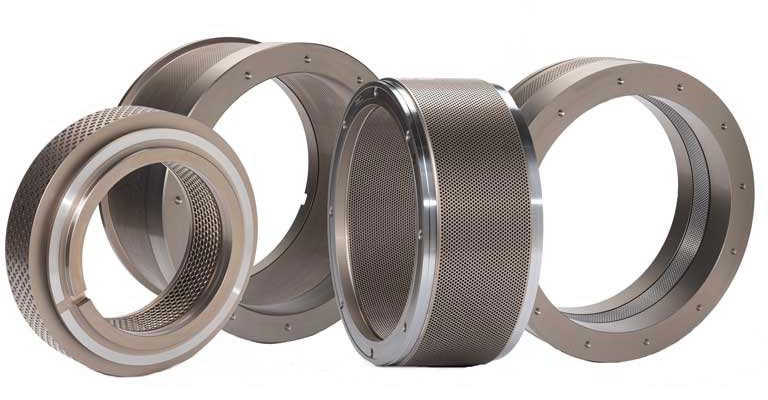
(1) Formüllerin tasarımı ve organizasyonu, toplamın yaklaşık %40'ını oluşturan su yemi peletlerinin kalitesi üzerinde doğrudan bir etkiye sahiptir;
(2) Ezilme yoğunluğu ve parçacık boyutunun düzgünlüğü;
(3) Halka kalıbının çapı, sıkıştırma oranı ve doğrusal hızı, parçacıkların uzunluğu ve çapı üzerinde etkilidir;
(4) Halka kalıbının sıkıştırma oranı, doğrusal hızı, söndürme ve temperleme etkisi ve kesme bıçağının parçacıkların uzunluğu üzerindeki etkisi;
(5) Hammaddelerin nem içeriği, temperleme etkisi, soğutma ve kurutma, bitmiş ürünlerin nem içeriği ve görünümü üzerinde etkilidir;
(6) Ekipmanın kendisi, işlem faktörleri ve söndürme ve temperleme etkileri, parçacık tozu içeriği üzerinde etkilidir;
3. Elleçleme önlemleri:
(1) Kumaş sıyırıcının uzunluğunu, genişliğini ve açısını ayarlayın ve aşınmış sıyırıcıyı değiştirin.
(2) Besleme miktarının az olması nedeniyle üretim başlangıcında ve sonunda kesme bıçağının konumunun zamanında ayarlanmasına dikkat edilmelidir.
(3) Üretim sürecinde, besleme hızının ve buhar beslemesinin istikrarlı olduğundan emin olun. Buhar basıncı düşükse ve sıcaklık yükselemiyorsa, zamanında ayarlanmalı veya durdurulmalıdır.
(4) Aradaki boşluğu makul bir şekilde ayarlayınsilindir kabuğu. Yeni kalıbı yeni silindirlerle takip edin ve baskı silindiri ve halka kalıbının aşınmadan kaynaklanan pürüzlü yüzeyini derhal onarın.
(5) Halka kalıbının kılavuz deliğini onarın ve tıkalı kalıp deliğini derhal temizleyin.
(6) Halka kalıbı sipariş edilirken, orijinal halka kalıbının eksenel yönünün her iki ucundaki üç sıra deliğin sıkıştırma oranı, ortadaki orandan 1-2 mm daha küçük olabilir.
(7) Mümkün olduğunca keskin bir kenar sağlamak için, kalınlığı 0,5-1 mm arasında kontrol edilen yumuşak bir kesme bıçağı kullanın, böylece halka kalıbı ile baskı silindiri arasındaki geçme hattında olur.
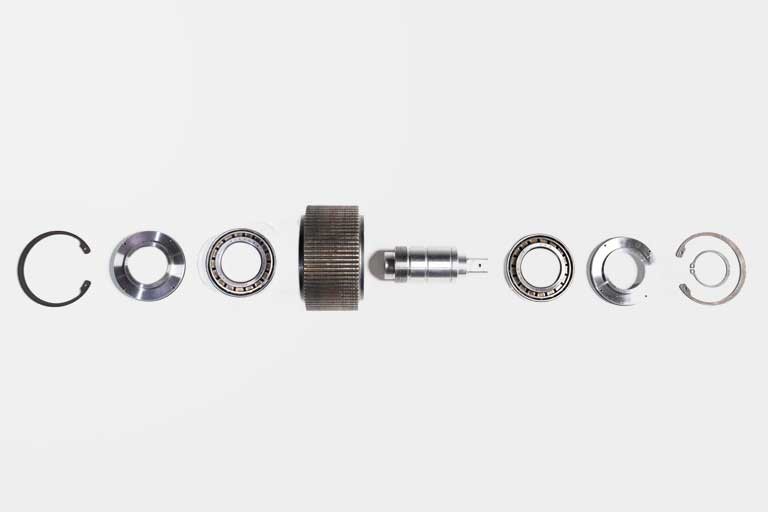
(8) Halka kalıbının eş merkezliliğini sağlayın, granülatörün mil boşluğunu düzenli olarak kontrol edin ve gerekirse ayarlayın.
6、 Özet Kontrol noktaları:
1. Öğütme: Öğütme inceliği, şartname gereksinimlerine göre kontrol edilmelidir.
2. Karıştırma: Uygun karıştırma miktarını, karıştırma süresini, nem içeriğini ve sıcaklığı sağlamak için hammadde karıştırma işleminin düzgünlüğü kontrol edilmelidir.
3. Olgunlaşma: Şişirme makinesinin basıncı, sıcaklığı ve nemi kontrol edilmelidir.
Parçacık malzemesinin büyüklüğü ve şekli: Sıkıştırma kalıpları ve kesme bıçaklarının uygun özellikleri seçilmelidir.
5. Bitmiş yemin su içeriği: Kurutma ve soğutma süresi ve sıcaklığının sağlanması gerekir.
6. Yağ püskürtme: Yağ püskürtme miktarının, nozul sayısının ve yağın kalitesinin hassas bir şekilde kontrol edilmesi gerekir.
7. Eleme: Malzemenin özelliklerine göre elek boyutunu seçin.
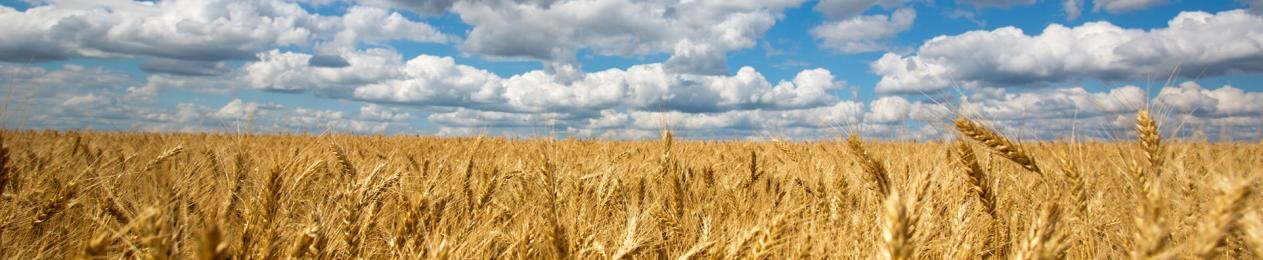
Gönderim zamanı: 30-11-2023